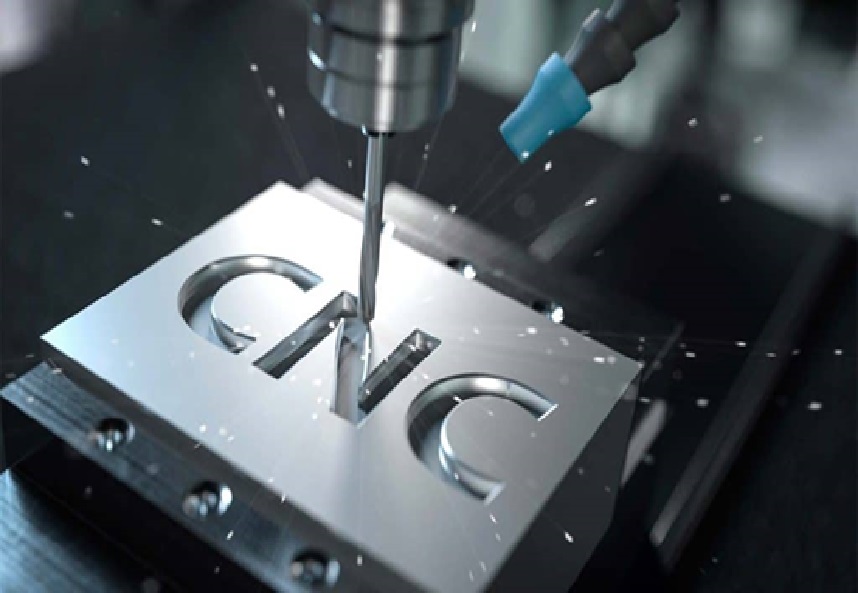
Selecting the appropriate number of axes for CNC milling can have a big impact on your output. The three most common options—3-axis, 4-axis, and 5-axis CNC milling—offer different levels of precision, complexity, and efficiency.
Understanding the advantages of each can help you make the best decision for your specific manufacturing requirements.
3-Axis CNC Milling
The simplest type of milling is 3-axis CNC milling. The tool may move from left to right, forward to backward, and up and down thanks to the machine’s three axes of operation (X, Y, and Z). This type of milling is ideal for flat, relatively simple parts and is commonly used in industries such as automotive and consumer goods.
Advantages of 3-Axis CNC Milling:
- Cost-effective: Compared to 4- and 5-axis machines, 3-axis machines are usually less expensive to buy and maintain. Additionally, they often have reduced operating expenses.
- Easy to program: Due to the simpler movement of the tool, programming is more straightforward, making it a good choice for companies with lower-complexity parts.
- Good for simple geometries: Ideal for parts that require flat surfaces, holes, and pockets, 3-axis machines offer precise control for basic tasks.
Disadvantages:
- Limited flexibility: Since 3-axis milling can only move along three planes, it cannot handle complex parts that require CNC machining from multiple angles.
- Longer production times: For more intricate designs, the machine may require several setups, which increases production time.
4-Axis CNC Milling
4-axis CNC milling adds a rotary movement (typically referred to as the A-axis) to the existing X, Y, and Z planes. This enables the workpiece or the tool to rotate, which facilitates accessing various parts without the need for human repositioning. When making more complex parts, this capability is really helpful.
Advantages of 4-Axis CNC Milling:
- Enhanced capability: The additional axis allows for more complex shapes to be machined in a single setup, improving production efficiency.
- Better accuracy: Error risk is decreased and accuracy is increased by eliminating the requirement for several settings.
- Time savings: The ability to rotate the part or tool reduces the need for part repositioning, saving both time and labor.
Disadvantages:
- Higher cost: 4-axis machines are more expensive than their 3-axis counterparts, both in terms of initial investment and maintenance.
- Complex programming: With the added rotary axis, programming becomes more complicated, requiring skilled operators and advanced software.
5-Axis CNC Milling
The most complicated and precise CNC milling machines are 5-axis models. In addition to the three traditional axes and a rotary axis, a second rotary axis is introduced, allowing the tool or workpiece to tilt. This enables the machine to reach nearly any angle, making it ideal for producing highly intricate parts.
Advantages of 5-Axis CNC Milling:
- Greater precision:5-axis machines can create components with intricate details and complicated geometries in a single setup, removing the need for repositioning and lowering the possibility of mistakes.
- Versatility: These machines are employed in fields where extreme precision and minute details are crucial, such as aerospace, medical devices, and automobile manufacture.
- Reduced lead times: Since parts can be machined in a single setup, production times are shorter, even for highly complex components.
Disadvantages:
- High cost: 5-axis machines are expensive and require a large financial outlay. The costs of operation and maintenance are considerably higher.
- Difficult programming: The complexity of programming and operating a 5-axis machine requires highly skilled operators and advanced software, which can increase labor costs.
Choosing the Right Milling Machine
Deciding which CNC milling is best for your production needs depends on the complexity of your parts, your production volume, and your budget.
- 3-axis milling is perfect for basic parts and organizations aiming for a more economical solution.
- 4-axis milling offers more flexibility and can handle more complex parts, reducing production times by requiring fewer setups.
- 5-axis milling provides the ultimate in precision and capability, allowing for the creation of highly intricate parts in a single setup.